Steel vs Concrete Staircases
What is the difference between a steel and a concrete staircase construction?
Firstly, there are two types of concrete staircases, the first being a pre-cast and the second being in-situ pour.
Pre-cast: This is when the complete staircase is formed and cast off site, and can generally only be used on new builds when the roof is off and the staircase can be lifted into position with a crane through the roof, but if the property is large enough it can be fitted with a spider crane if there is large enough access into the building.
In-situ pour: This is done when a staircase mould is made up on site, mostly from timber formers to form the shape, rise and going of the staircase, then steel reinforcement bars are threaded into the mould and its filled with concrete, the timber formers are then broken away.
Steel staircase: There are many shapes, sizes and designs available, and the design can be changed to either a complete modular staircase that can be installed in-one piece or it can be dismantled into multiple items to enable it to fit through and into small areas such as lifts, narrow corridors or small entrance doors etc and then assembled in position.
What practical considerations should be taken into account before choosing either of these two materials?
There is an expression that says “begin with the end in mind” and many a time due to time restraints construction companies tend to rush through the 1st fix items in view of the design/ connections and tolerances hopefully being addressed/sorted within the 2nd fix – We often see that a concrete staircase has been fitted early for access and often no thought has gone into how the balustrades will connect to it or handrails will flow or floor finishes will fit to the concrete staircase.
Some key things to consider:
- Can the building take the weight of concrete?
- Has consideration been made for building regulations? Number of treads/ half landings – enough room to extend the handrail past the end of the treads etc etc
- Will a timber staircase suit? – Are there large spans or unsupported returns that may make timber unsuitable?
- Will the staircase be adjacent to a wall? (this enables fixings into the wall for strength and reduces the sizes of the materials required)
- Do you require open risers? (not possible in concrete and sometimes timber hasn’t the core strength)
- How will the balustrade fix to the staircase? How will the treads or soffits finish against the balustrades? Is concrete or steel a better connection?
- Will any lighting/wiring be run in the staircase? Wiring routes?
These are some of the common issues we see, but it’s always worth discussing the initial design with a staircase specialist to look at possible restraints & options.
Off-site construction options:
- With a steel staircase it can all be made off-site and removes a lot of the need for site works – Steel staircases are fully trial built off-site including the balustrades to ensure a perfect fit, reducing time, and labour on-site, improving level of quality and enabling off-site inspection before site arrival – The balustrades are then stored off-site to be installed when site is ready, this saves any damage to the balustrades and removes the need for late program works. – all connections between balustrade and staircase are pre-agreed allowing the following stone tread companies to scribe over the connection holes and drill the stone without on-site scribing, reducing personnel on site, leading edge issues, stone breakages, setting out mistakes etc.
Misconceptions of steel staircases:
Not as strong as concrete and deflection issues?
- This is mostly down to poor steel designs, at Alpine we have the capability to remove the deflection concern.
Expensive?
- When account is taken of the risk and extra management time to coordinate, the initial cost difference is irrelevant and the advantages are obvious.
What are the common issues found when installing to concrete:
- We often find concrete staircases are fitted to 1st fix tolerances and not aligned to the required margins. – this is either its too tight to a wall resulting in finger traps, or the staircases are not aligned to each other, or the floor to floor heights are not within tolerance resulting in the top and bottom step being different height.
- Retro fitting balustrades on-site results in costly and slow drilling of concrete to form connections, large amounts of personnel on the staircases resulting in site frustration, trip hazards and lower quality of finishes.
- Often the drilling required to install the balustrade hits the rebar reducing its strength and structural integrity.
- Difficult to prove connections with structural calculations as it relies on the integrity of the concrete pour.
- Steel balustrades cannot be surveyed until the stone treads are installed (due to experience that the treads and risers rarely follow/shadow the concrete stair accurately) and often the stone isn’t laid until the last weeks/ months of the project leaving a very short window to measure up, fabricate the balustrades.
- Timings – Often we are asked to survey the concrete staircase and make allowance for the stone finishes, more often than not the stone treads do not shadow the concrete staircase exactly, due to either inconstant concrete staircase, or its been installed out of tolerances and the stone finishes are used to remove the inconsistency resulting in the balustrades not fitting to the stone finishes accurately and again last minute alterations.
Why steel from the end users perspective:
- Removes potential delays.
- Early involvement gives time to consider design options.
- Insures approved connection designs, no surprises.
- Improved quality of balustrade connections.
- Less people on site reducing risk of damage elsewhere.
- Offsite construction reduces travelling and environmental impact.
- Safer site conditions.
- Cost neutral, it just requires a change of mindset.
Contact us for a steel staircase on your next project!
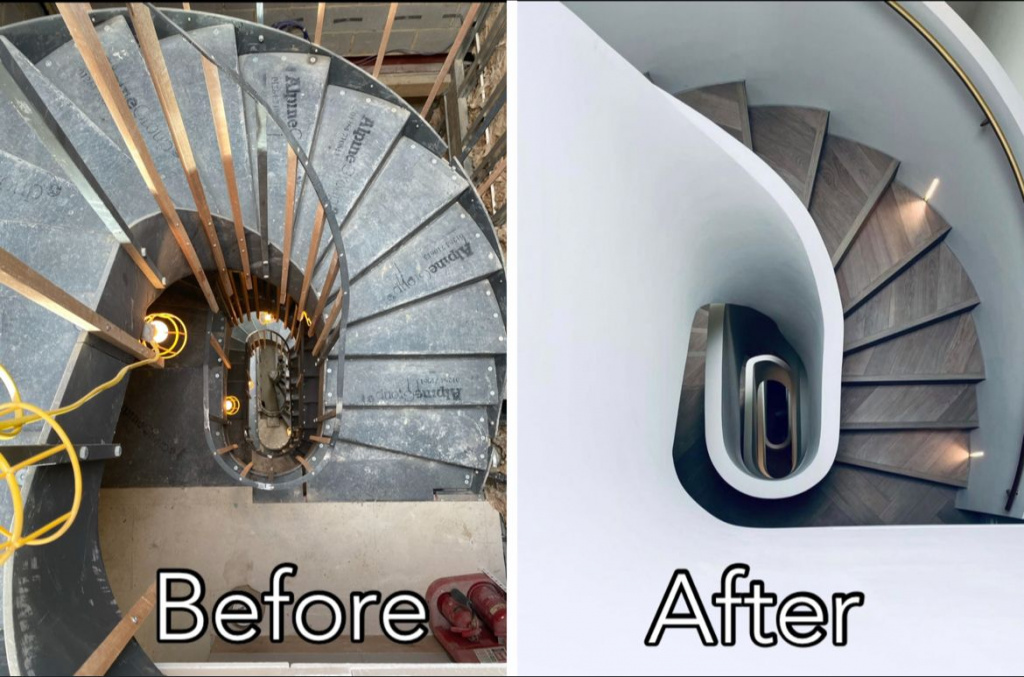